Prototyping: A Key Step in Product Development
13 December 2024
Uncategorized , Industrial equipments , Consumer products , Medical , Transport
4 Min
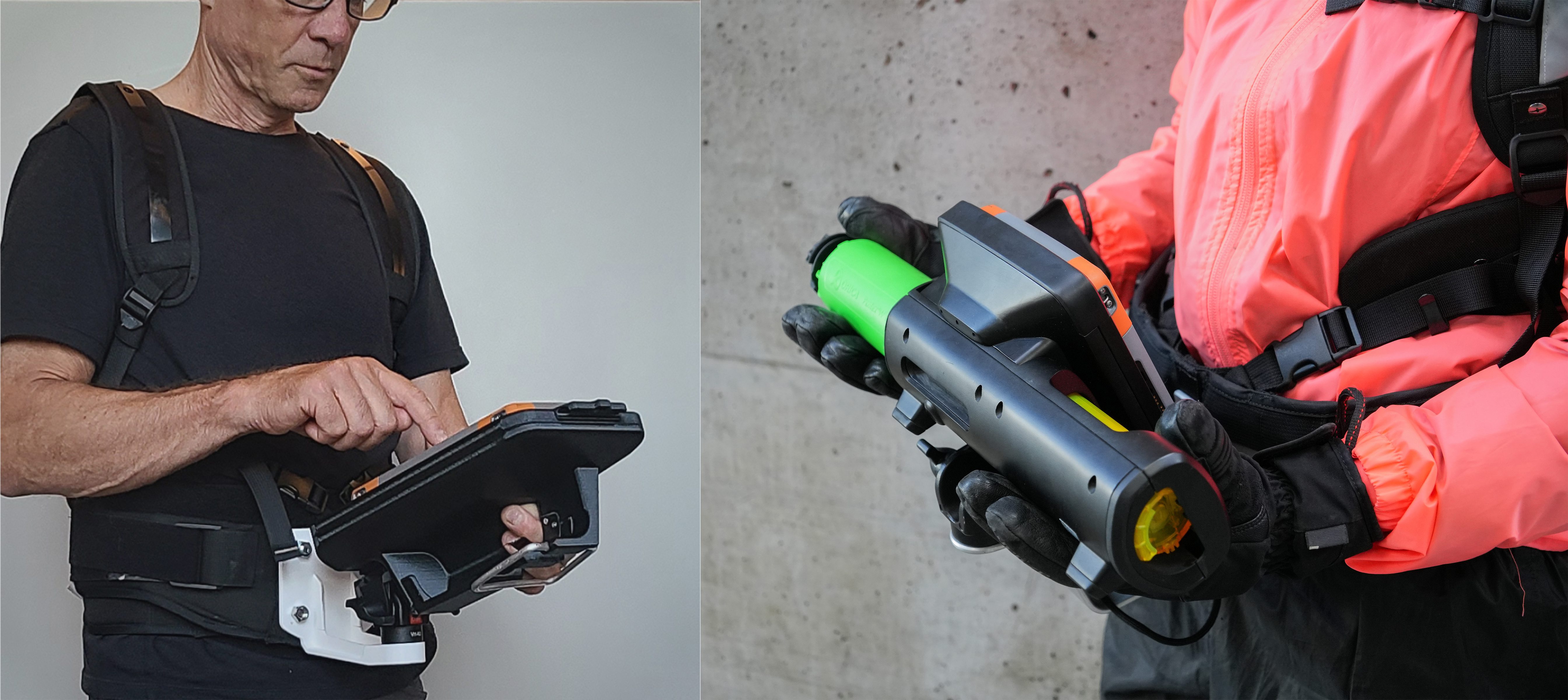
Prototyping: A Key Step in Product Development
Prototyping is a fundamental tool for quickly identifying potential challenges and turning ideas into tangible products. While digital models are useful, physical prototypes provide a more concrete understanding and a comprehensive validation of a product’s success. At Alto, the wide variety of prototypes we develop not only reflects our expertise but also demonstrates our ability to meet diverse client needs with innovative and tailored solutions.
Early Problem Detection
Incorporating prototyping early in the product development process is essential, as it provides a tangible first iteration of the product. “In 90% of cases, when the first model is made, we realize it’s either larger or smaller than imagined,” explains Patrick Mainville, President of Alto. He adds that the initial model, often crafted from cardboard or foam core, allows the team to quickly discuss the product’s architecture and make informed decisions to guide its evolution.
“A prototype can be basic yet functional,” he continues. “It enables the team to learn how to use the product effectively and resolve certain issues at a low cost—which is exactly what we aim for.”
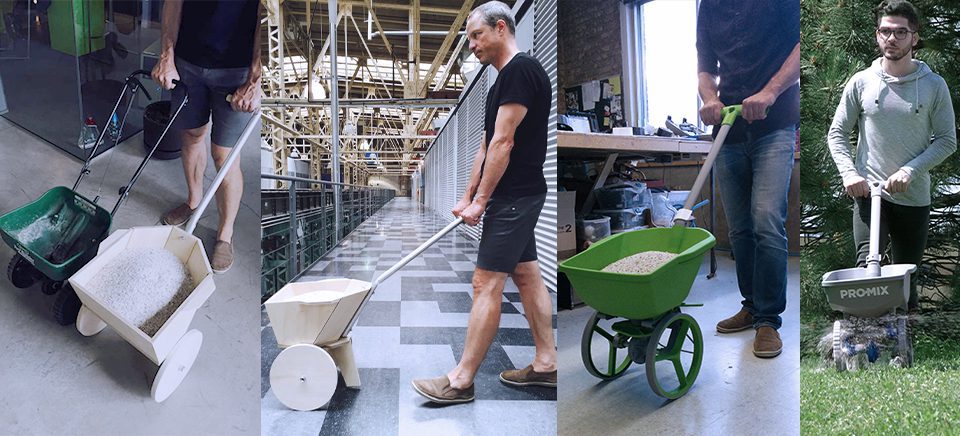
By handling a physical prototype, designers and engineers can better evaluate the product’s size, weight, and ergonomics. This iterative process uncovers subtle but significant aspects that may not be evident in digital 3D models. Easy to modify, an initial volumetric model evolves into a functional prototype and eventually into a presentation prototype.
Validation on a Human Scale
Working with a physical model also helps assess grip, balance, and the impact of various loads. “It’s more beneficial to create a simpler prototype earlier and iterate through multiple versions than to wait and produce a more complex one later,” asserts Benoit Orban, senior industrial designer at Alto. ” There are functions we want to “derisk” in a planned way, but also other aspects that we’ll discover through the prototype,” he adds. This is why early prototyping is crucial.
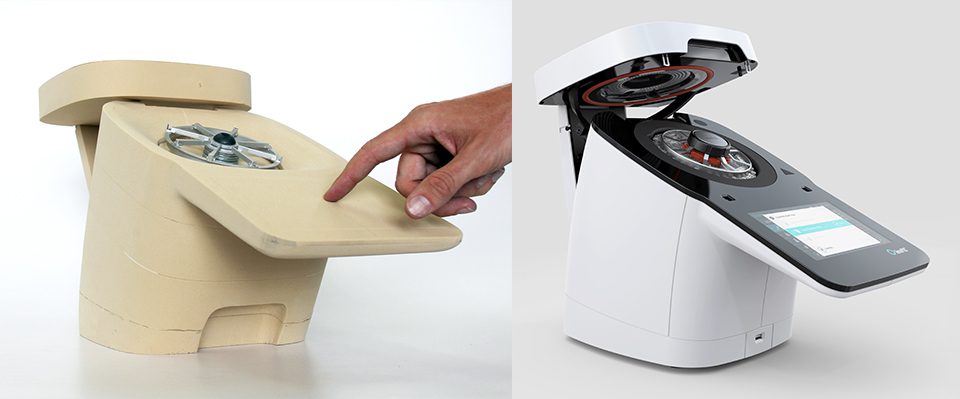
For larger products, Orban emphasizes the importance of accessibility tests in real-world scenarios. These tests provide invaluable insights for adjusting the product’s dimensions and features. “Through prototyping, we simulate elements that will come into play later in development. We can also test lighting and brightness levels, which can influence color choices and user understanding,” he notes.
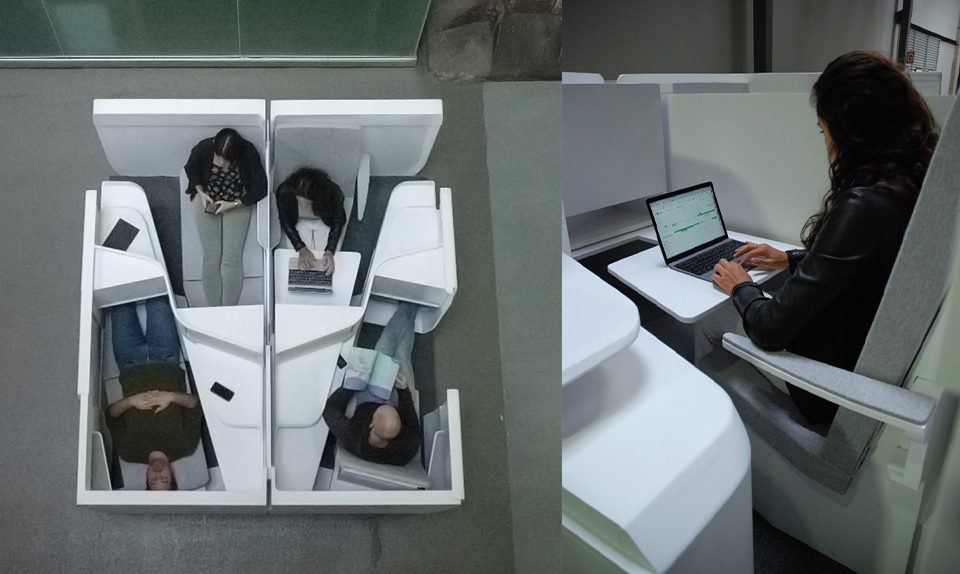
Prototyping also validates material choices, visual effects, assembly methods, and optimizes the number of components used. Models are particularly effective for client presentations and focus group testing. In a co-creation context, target users are more likely to share observations when interacting with a tangible version of a product. “By the time the presentation prototype is complete, we know it will work well, impress visually, and meet user expectations,” Orban highlights.
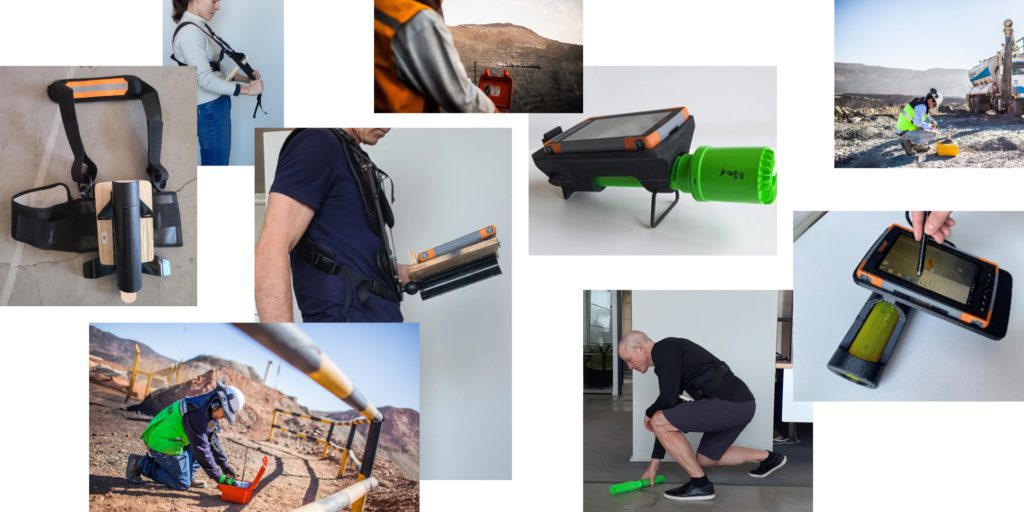
The Essential Role of the Model Maker
The model maker bridges the gap between ideas and the physical realization of prototypes in the workshop. Their involvement in finding solutions brings invaluable technical expertise and concrete suggestions that guide the project in the right direction.
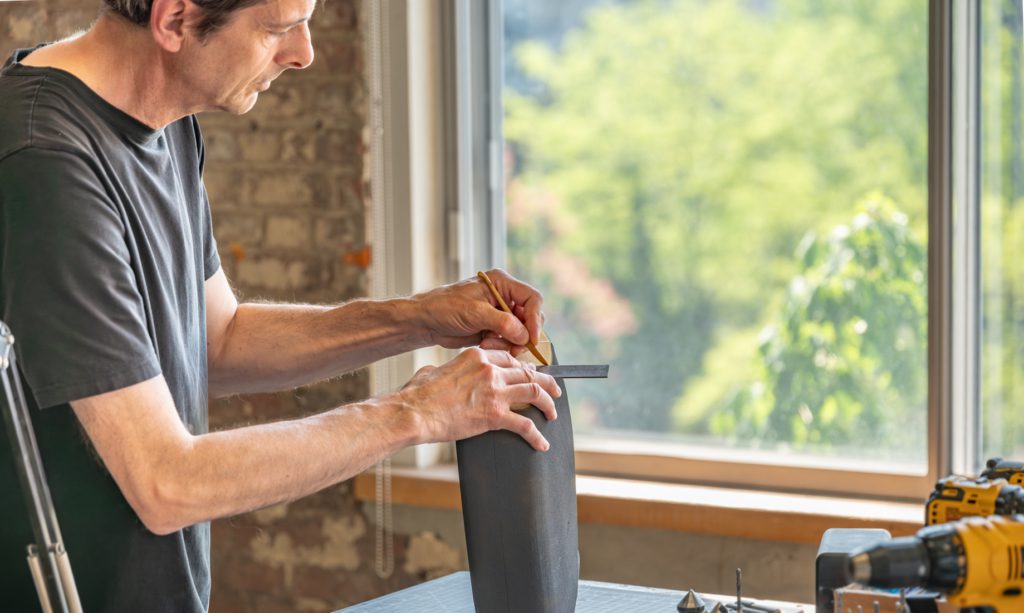
“Whether the prototype consists of components made by our model maker or assembled from external suppliers, we uncover elements that might have remained blind spots until that point,” says the designer.
This continuous interaction ensures necessary adjustments are made efficiently, often within the same day, without needing to go back to the drawing board. Complementing digital tools, the model maker’s work guarantees an optimal design process.
“In post-project reviews, nine times out of ten, we realize we should have prototyped more during the project.”
Patrick Mainville, President of Alto
Saving Time and Money
Identifying issues early prevents costly errors during the production phase, such as modifying injection molds. By adopting a “fail fast” approach, teams can quickly validate concepts, gather immediate feedback, and make necessary adjustments before committing to significant investments. Patrick Mainville encourages businesses to invest more in prototyping: “Prototyping more means innovating more simply and efficiently,” he concludes.